Latest News & Blog
Catch up with the latest energy news and information
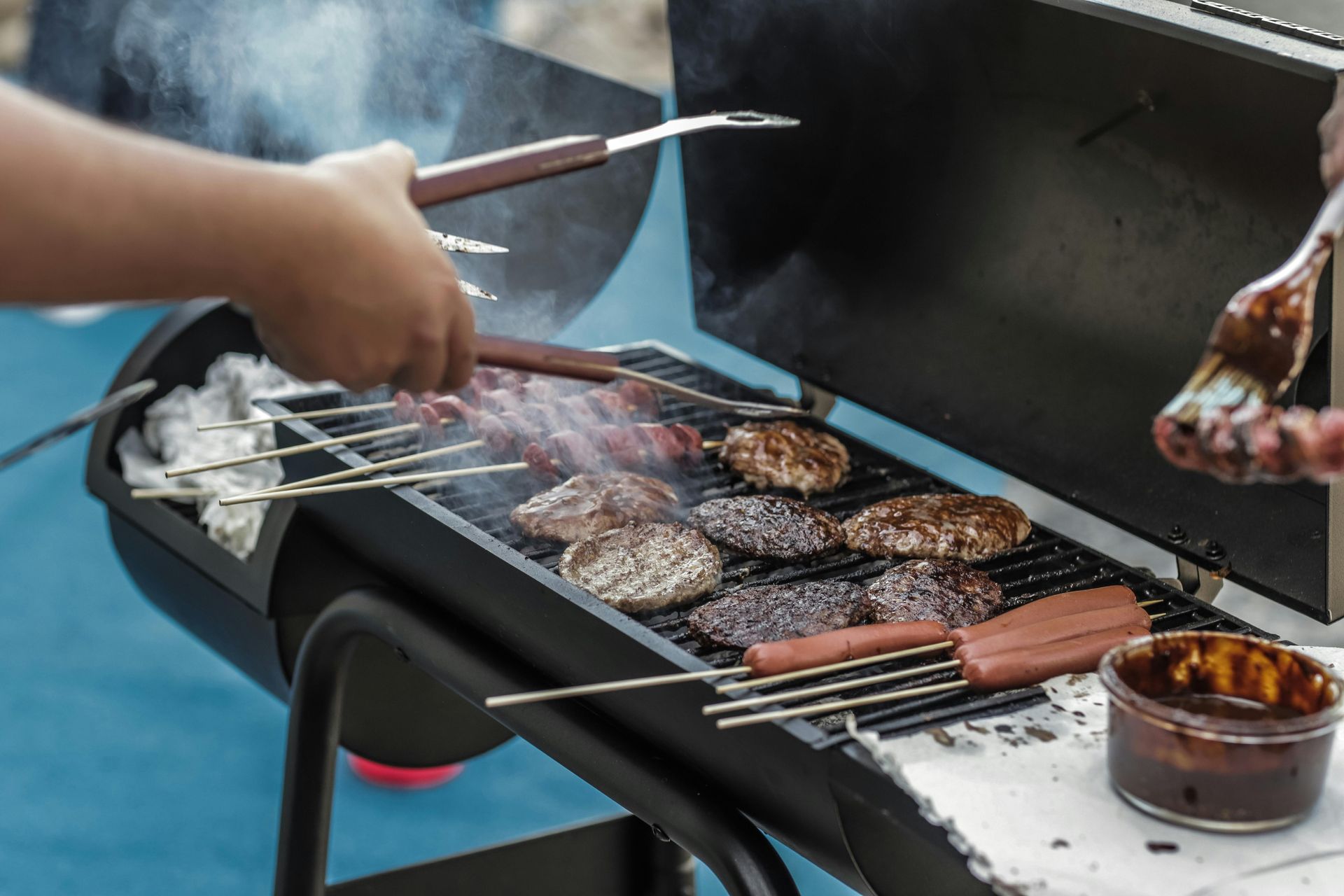
June 2025 Review By Adam Novakovic The British summer is underway and it commenced with a heatwave, leading to record temperatures during the opening games of Wimbledon. However, energy prices would be largely dictated by events far away from the UK, as a need for cool heads in the Middle East was the primary driver of energy prices throughout June.
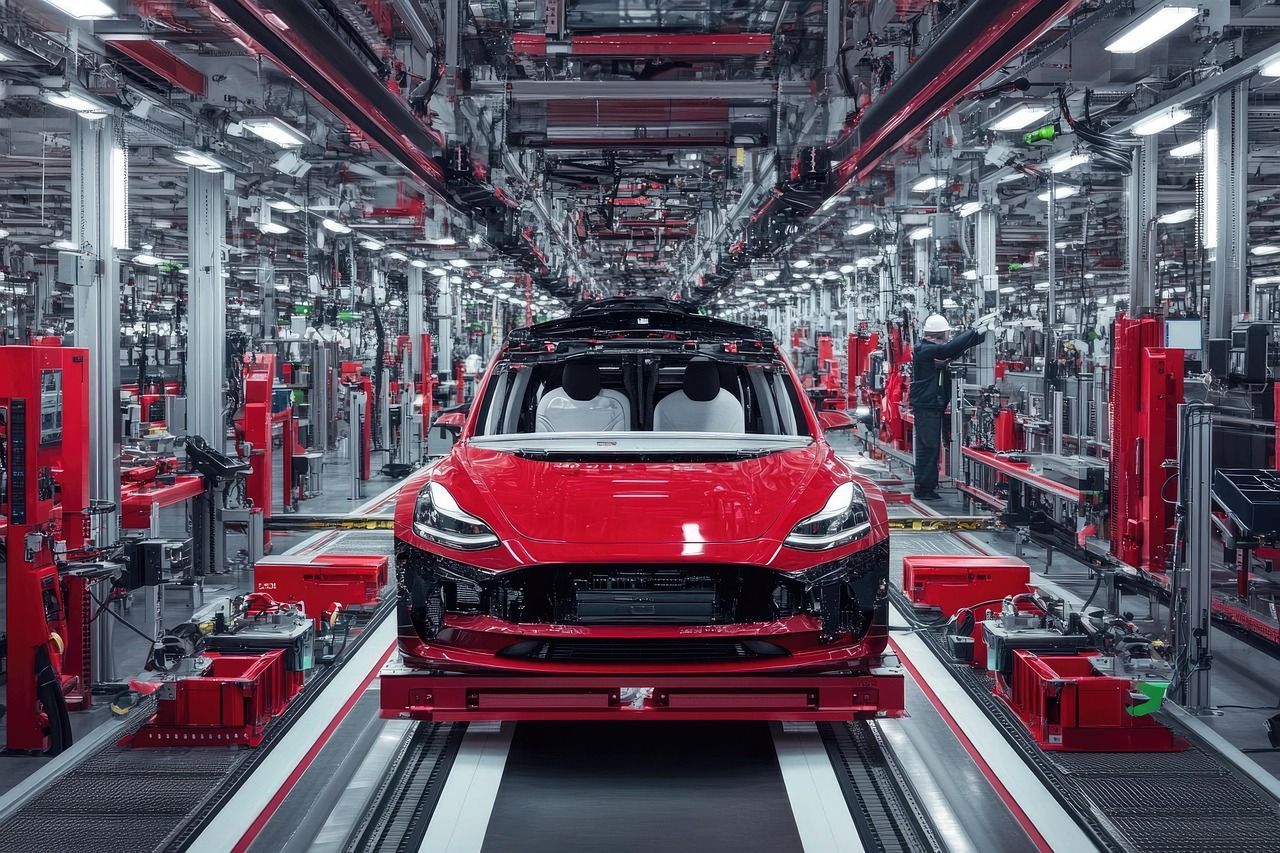
The UK's Modern Industrial Strategy 2025 Electricity Discounts for Over 7,000 Businesses Thousands of UK businesses are set to benefit from a new government plan to cut energy costs, boost competitiveness, and support long-term industrial growth. As part of the newly launched Industrial Strategy, electricity bills for over 7,000 energy-intensive firms will be cut by up to 25% from 2027. What Is the UK's Modern Industrial Strategy? Unveiled on 23 June 2025, the government’s 10-year Industrial Strategy is designed to stimulate business investment, create over one million skilled jobs, and address key structural barriers that have hindered British industry — particularly high electricity prices and delays in grid connections. Central to this plan are two new policies focused on reducing energy costs for businesses: The British Industrial Competitiveness Scheme (BICS) An expanded British Industry Supercharger programme
How the Iran-Israel Conflict Could Impact UK Energy Prices By Adam Novakovic Tensions between Iran and Israel have intensified in recent weeks, prompting renewed concerns across global energy markets — including in the UK. The immediate impact has seen some fear in the markets and prices have risen as a result. Any further signs of escalation that could disrupt global supply routes will likely provoke sharp spikes in wholesale energy prices. Soon after Israel launched initial attacks and Iran responded, the United States distanced itself from Israel’s aggressive military posturing, urging both sides to engage in diplomatic dialogue and to avoid an extended regional conflict. This initial reluctance to support a drawn-out confrontation has helped calm fears of a broader war, however, there have been some indications that the US position could change. If the US were to become more directly involved, then the outlook would worsen considerably. US involvement would increase the probability of ground troops being deployed in Iran, and of a prolonged war. Without prolonged hostilities, the energy market should resume its downward trajectory once immediate geopolitical risks fade. Both Iran and Israel lack the resources to sustain a protracted war without foreign support, and most analysts agree that military actions will likely remain confined to missile exchanges, drone activity, and cyber or intelligence-based sabotage, rather than a full-scale ground war.
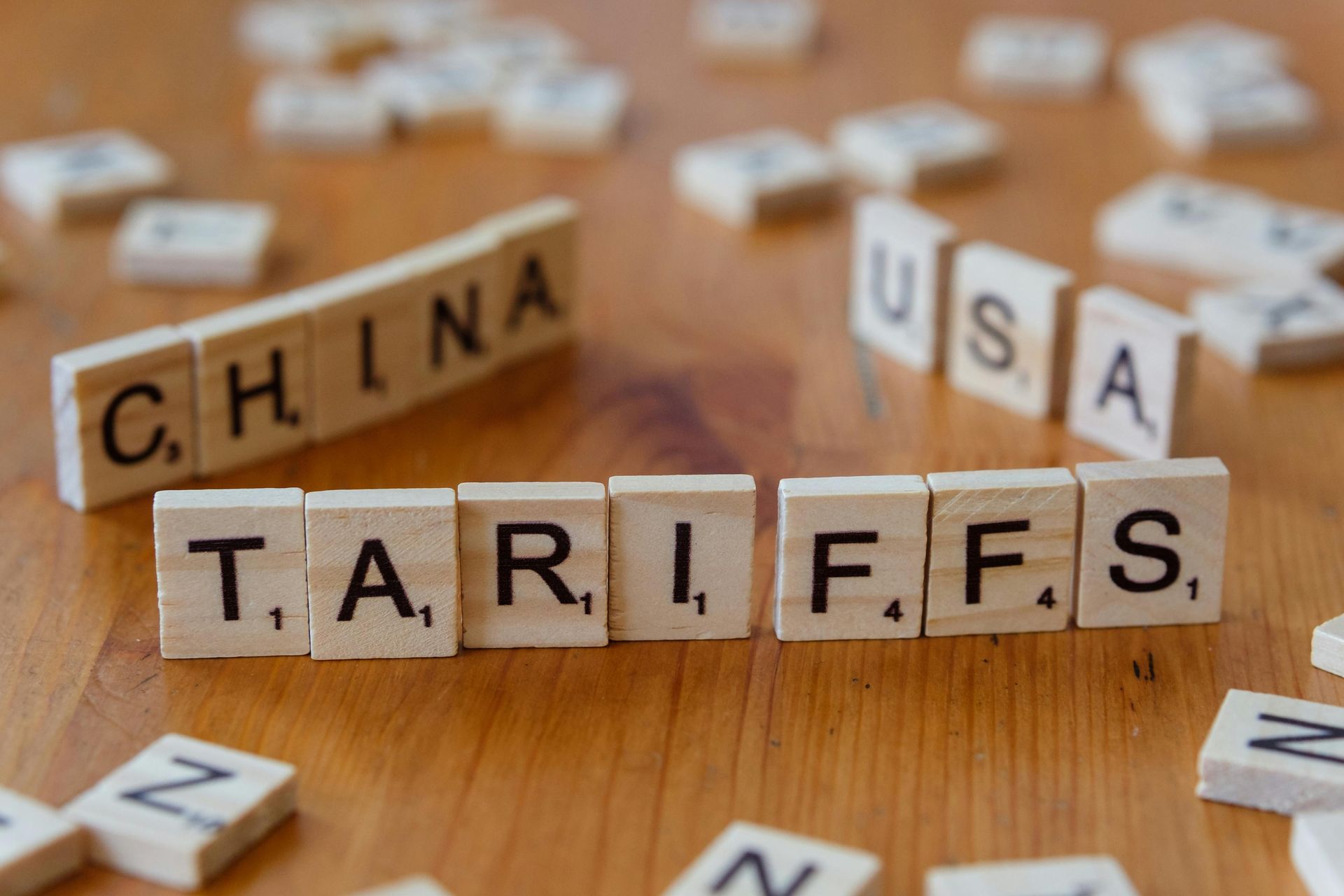
April 2025 Review By Adam Novakovic For some, April can be the cruellest of months. We saw Earthquakes cause damage in Thailand, volcanic eruptions near Iceland, and the month ended with blackouts in the Iberian peninsula. The latter highlighting the issues with switching to renewable energy sources too quickly, at the expense of energy grid stability. However, April can also be a time of great optimism as we exit the winter months and head towards the summer. The energy markets gave us plenty of reasons to be happy in the past month as wholesale gas prices fell over 20%. This drop was also seen in the gas markets for Winter’25 (a 20.42% drop) and for Summer’26 (a 14.17% drop) as prices fell, representing a good buying opportunity for those on flexible contracts.
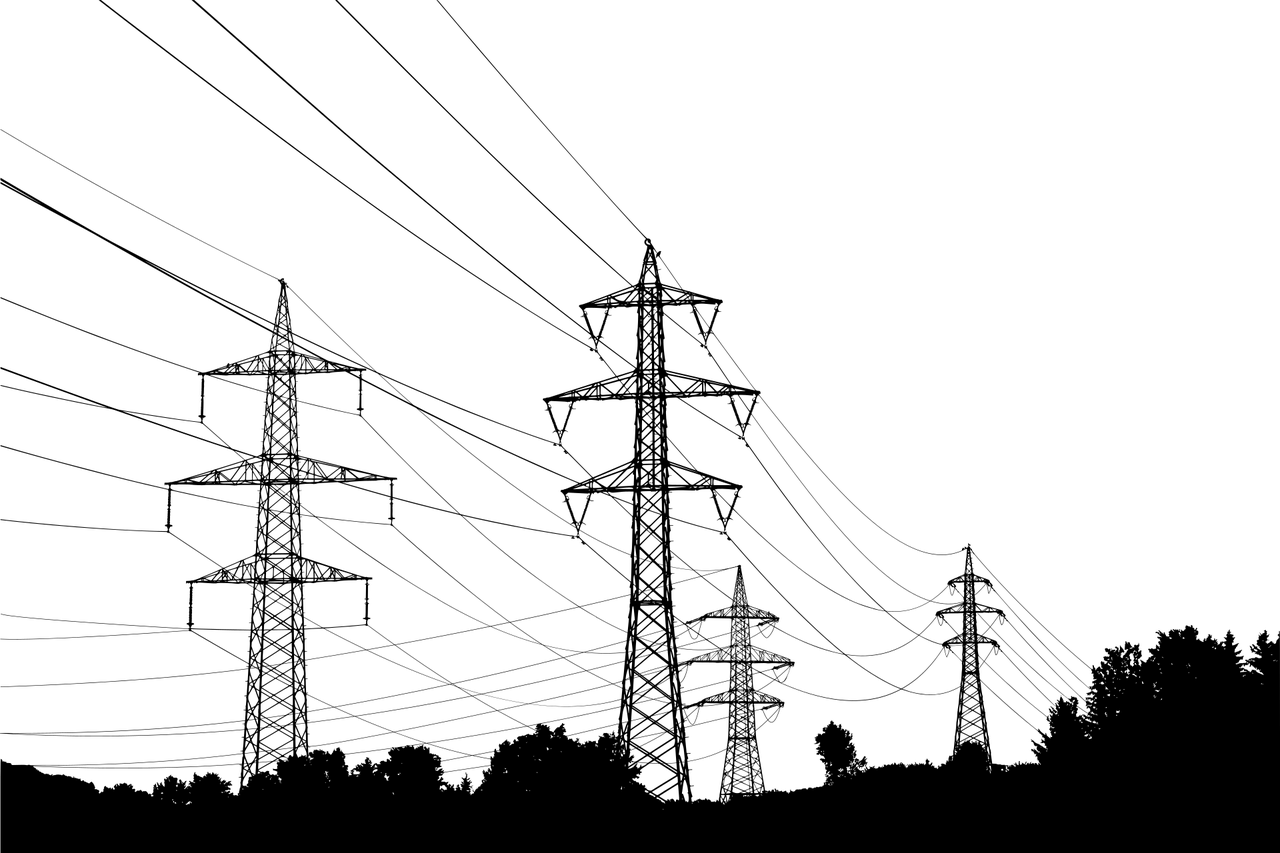
TCR Banding: A Powerful but Overlooked Way to Lower Energy Costs for UK Businesses As UK business energy prices continue to fluctuate at historically high levels, companies across the country are under increasing pressure to find reliable ways to lower energy costs. With government levies, non-commodity charges, and market instability all contributing to rising bills, businesses must now look beyond traditional energy-saving methods to manage their expenses. In previous articles we looked at how to lower kVA charges , and published a guide on how to lower business energy costs . One such method gaining attention is TCR Banding — a relatively lesser-known, yet impactful solution for reducing DUoS and TUoS charges. What Is TCR Banding? TCR Banding is part of the Targeted Charging Review (TCR) , a reform introduced by Ofgem in 2022. Its goal is to ensure a fairer, more consistent system for charging UK electricity users for their share of the grid's maintenance costs — specifically the Transmission Use of System (TUoS) and Distribution Use of System (DUoS) charges. Instead of charges being based on when energy is used (which could be manipulated by large users), charges are now fixed and based on how much energy is typically consumed. This is where TCR Bands come into play. What Are TCR Bands? TCR Bands categorize electricity meters into different levels based on their voltage type and agreed kVA capacity. These bands determine the fixed DUoS and TUoS charges applied to a business's energy bill. For Low Voltage (LV) Half-Hourly Meters: Band 1: 0 – 80 kVA Band 2: 81 – 150 kVA Band 3: 151 – 231 kVA Band 4: 232 kVA and above For High Voltage (HV) Half-Hourly Meters: Band 1: 0 – 422 kVA Band 2: 423 – 1,000 kVA Band 3: 1,001 – 1,800 kVA Band 4: 1,801 kVA and above The higher your TCR band, the more you'll pay in fixed DUoS and TUoS charges — making it essential for UK businesses to ensure their banding is correctly assigned. Who Assigns Your TCR Band? Your Distribution Network Operator (DNO) is responsible for assigning your TCR Band. DNOs are regional companies that manage the physical infrastructure delivering electricity to your site. They’re also the ones compensated through DUoS and TUoS charges shown on your business energy invoice.
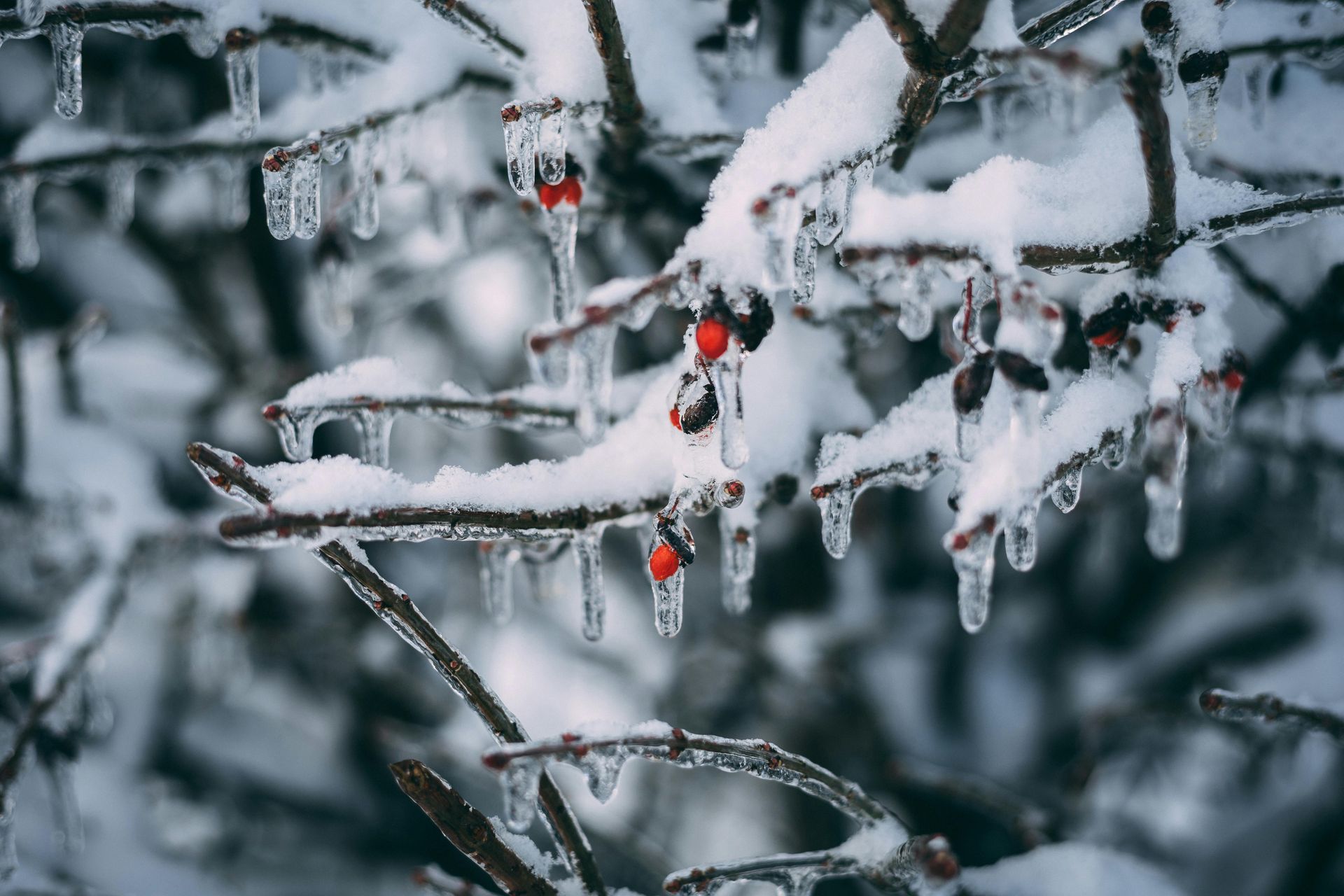
January 2025 Review By Adam Novakovic This January saw the UK record it’s coldest night in 15 years, but there wasn’t much in the way of wind to accompany the cold temperatures of the month. This combination led to more energy being used than expected and lower-than-hoped renewable levels being recorded, as energy prices continued to rise against the backdrop of European gas reserve levels being depleted. January kicked off with the long-expected news that Russian gas supply would cease flowing into continental Europe. Whilst the cessation of this supply had been long planned for, many would have hoped it wouldn’t coincide with a cold snap hitting the continent. The lower-than-expected temperatures have led to energy consumption being higher than anticipated putting a further strain on reserve supplies. While the weather forecasts were making for dim reading, there was some positive news coming from across the Atlantic. Donald Trump -- uncharacteristically for a politician -- had followed through on his pre-election promises and lifted the freeze on US LNG exports. In addition to reallowing exports to be permitted, Trump has also allowed for new US LNG projects to be applied for, this boosts both short and long-term positivity surrounding the gas supply that can be received by Europe. With the cessation of the Russian gas supply occurring instantly from January 1 st , and the restarting of US exports being something that will likely take months before export capacity is fully ramped up, it could be a few months before the positive effects are truly felt. This would coincide with the end the European winter, so it may be the end of March or beginning of April until the market has a more positive response. However, this could also be when European nations look to begin restocking their reserves. For those with renewals in the coming 3 months, now may be the best time to seek prices, as the further depletion of European gas reserves is likely to have a negative impact upon prices. For those whose contract is due for renewal later in the year, it may be best to be patient and wait for the market conditions to change. If your contract is due for renewal later this year and you would like a reminder sent when the market conditions turn more favourable, simply email your contract end date to adam@seemoreenergy.co.uk and we will provide reminders ahead of the renewal, at times when the market is presenting favourable negotiation conditions.
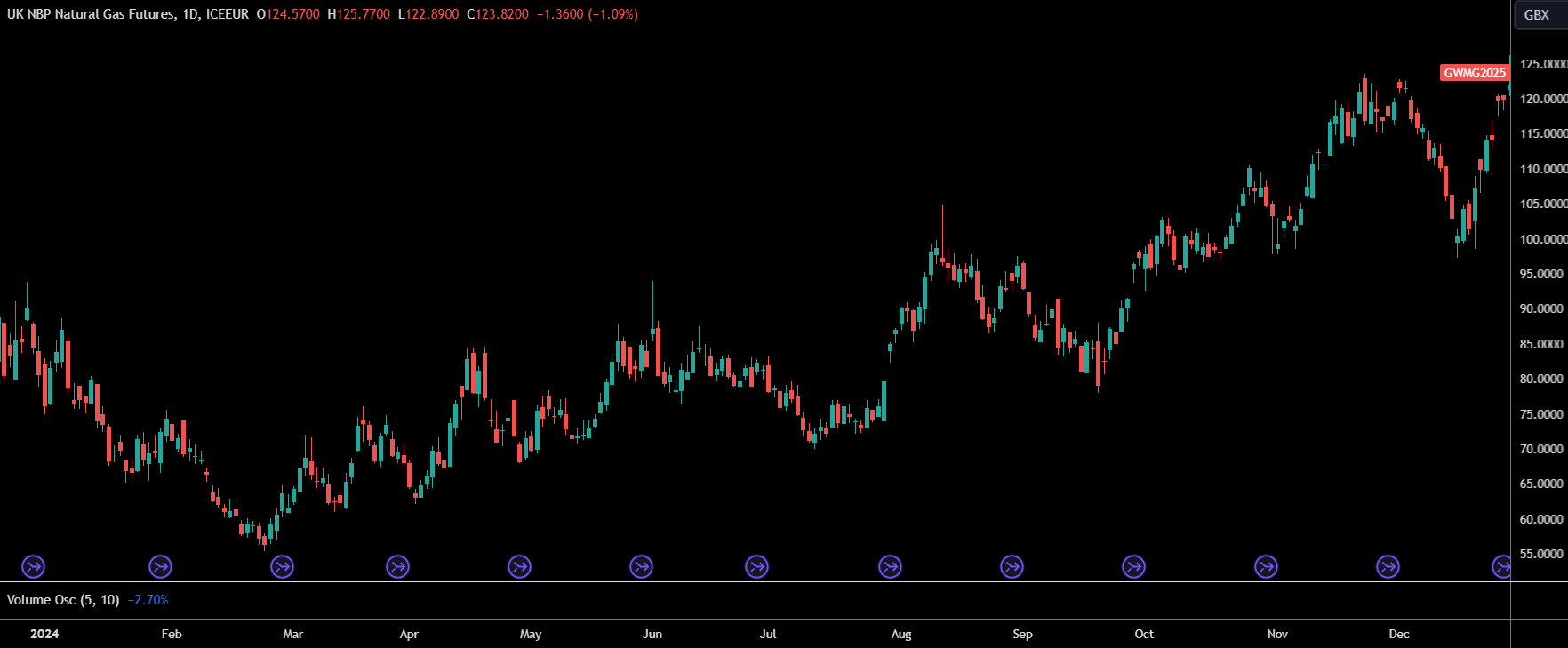
2024 Review By Adam Novakovic In a year that began with falling energy prices, there were recurring catalysts that led to prices climbing steadily higher. Geopolitical uncertainty and the perennial threat of escalating conflicts meant fear would maintain a constant presence in the wholesale markets. We will look back at the key energy stories from 2024, and how the energy markets are likely to shape up in 2025. Quarter 1 The year began with cautious optimism as the UK’s gas reserve levels were healthy and prices for the Summer’24 season were in freefall. In February, prices pulled back to their lowest levels since 2021, and for the first time in a while, we identified that there was greater potential for upside risk than for further downward price movement: “ there now (exists) an asymmetrical element of risk should the market encounter a supply-side problem of significance. ” During February we had advised customers on flexible contracts that this was an ideal time for making purchases. March would see prices begin to ascend again as international conflict would create problems with LNG imports, and we would highlight the geopolitical risks as an area for concern moving forwards: “ fears remain and there are potential negative catalysts that could lead to prices rising further, with the main factors to watch out for being based on geopolitical unrest. “ For a business that purchases their energy in advance, this quarter was the optimal time for purchasing during 2024. In February, electricity prices for Winter’25 were down to 7.75p/Kwh, and as low as 6.05p/Kwh for Summer’25. Winter’25 ended the year with prices above 11.1p/Kwh, with Summer’25 prices exceeding 9p/Kwh. For a company that uses 500,000Kwh of electricity per month, the difference between buying at the February low point compared to today’s prices would represent a yearly saving of over £200,000.